株式会社タイヨーアクリス様 金属製品製造業MRP版
毎日8時間かかっていた生産計画と購買管理の作業が40分に短縮!
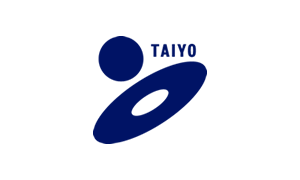
2007年4月、太陽機械工業株式会社の電機事業部を分社独立し設立された、金型設計製作からプレス加工まで行う電子部品メーカー。同業他社に先駆けたジャスト・イン・タイムにいち早く対応し、プレス技術を中心とした複合加工ラインや順送冷間鍛造ライン等のハード面と、品質管理・生産管理システムのソフト面の両輪により、フレキシブルなものづくり体制を確立されています。新システム開発から導入まで、どのような状況だったのかをお聞きしました。
株式会社タイヨーアクリス
取締役(製造・業務全般) 森 一郎 様
営業部 部長 藤村 俊明 様
営業部 主査 加藤 康寛 様
新システム導入の経緯
旧販売管理システムの老朽化と、時代のニーズに合わなくなった大量生産型から多品種少量生産への切り替えのため、2006年5月から新生産管理システムの開発を他開発ベンダーとスタート。しかし、システム設計に着手して間もなく、一時中断を余儀なくされました。
中断原因の一つ目は、社内プロジェクト体制にありました。PCに詳しいということを前提に人選をしましたが、実務に精通しているが決定権がない担当者や、決定権はあるが実務をよく知らない管理職で構成してしまったことです。二つ目は、依頼した開発ベンダーに製造業のノウハウが乏しかったことです。主体性がなく、しかもフルオーダーの開発であったため、要件定義の際に社内からの要望をそのまま受け入れてしまい、要件が絞りきれずに工数が膨れ、遂には開発ベンダーからお手上げの申し入れがありました。
その後、2007年8月にシステム開発を再開することになりました。再開にあたっては過去の苦い経験を活かし、以下の3つのポイントを押さえた社内プロジェクト体制作りから着手しました。
(1)トップダウン型組織
(2)各部署から業務に精通し、かつ実行力のあるメンバーを中心に選抜
(3)推進事務局を設置
システム選定のポイント
前回の失敗の影響による開発期間の短縮と費用面を考慮し、フルオーダーではなくパッケージソフトをベースに構築することに方針転換しました。パッケージの選定においては、外部のITアドバイザーを招き、Factory-ONE 電脳工場MFと他ベンダーソフトを含めた3製品の中から検討しました。
結果、EDI連携、MRP機能など生産管理システムの基本機能が充実していること、そして、ソースプログラムが公開されていることで自社カスタマイズができ、開発コストの抑制と短納期開発が可能なことから、若干予算はオーバーしますがFactory-ONE 電脳工場MFを採用しました。しかし、この段階で本稼働までに残された時間はわずか7カ月でした。
システムの導入において苦労した点
社長から特命を受け、プロジェクト推進責任者に任命されましたが、前職で工場立ち上げの経験があるとはいえ、生産管理の実務をこなしながら7カ月で新システムを本稼動させなければならないのは、かなり厳しいミッションでした(加藤主査)。そこでシステム開発の効率化のため、以下のポイントを重点にプロジェクトを推進しました。
(1)各部門からのヒアリングをもとに業務フローを作成し、ベンダーSEとの打合せ前には、必ず事務局と部門担当者との事前打ち合わせを実施
(2)現状フローとFactory-ONE 電脳工場MFでのフローのギャップを抽出し、最低限必要なカスタマイズ項目を検討。さらに、外部ITアドバイザーの「カスタマイズはシステムの幹になる部分を最優先(枝葉は後付)させること」というアドバイスも終始徹底させた開発プロジェクトの進行
各部門との打ち合わせを重ねる内に、カスタマイズ要求が膨れ、予算オーバーが想定されたのですが、ソースプログラムが公開されている利点を活かし、また、CrystalReportとObject Browser のスキルを取得し、簡単な帳票作成などは自社対応することで解決させました。
こうしたプロセスを経て、2007年12月に新業務フローとシステム設計書が完成。ここまでの道のりは相当な苦労もありましたが、幸い各部門から業務に精通し、かつ実行力のあるメンバーを選抜したおかげで、無事まとめ上げることができました。
その後、システム設計書が承認され、カスタマイズ開発をしている間に、プロジェクトでは以下の作業を順に進めました。
(1)マスター登録、整備
(2)業務毎に運用マニュアルを兼ねた操作手順書の作成
(3)入力担当者への操作指導
(4)仮稼働
(5)本稼働
今回のプロジェクトでは仮稼働から本稼働開始までの間が、特に苦労しました。仮稼働期間を2カ月はかけたいところでしたが、前システム開発の中断の影響により、わずか2週間というタイトなスケジュールで実施しなければならず、操作の習熟度不足による入力遅れの多発や、さらにマスター不備の発覚といった状況下で本稼働を迎えることになりました。本稼働開始後も、入力遅れが多発しました。そのためデータの信憑性が損なわれ、管理が困難になりました。仮稼働の準備不足が、本稼働後の新旧システム一発切替の障害となり、やむなく平行稼働期間を1カ月間延長せざるを得なくなりました。
旧システムの保守打ち切りは2008年4月末であり、これ以上のスケジュール延長は絶対に許されませんでした。そのため、入力遅れの原因となるメカニズムを徹底的に究明しました。そして、プロジェクトメンバーを中心にスタッフ全員が一丸となって対応に当たった結果、2008 年4月は受注が記録的に伸び、現場の負荷が極限にまで達していたにもかかわらず、1カ月後の5月に完全切替できました。
導入効果
旧システムでは、熟練者の知識と経験を駆使して8時間必要だった生産計画の立案から材料手配の業務が、新システムでは新人でも40分で実現できるようになりました。また、在庫管理においても
(1)前日の在庫が翌月の昼にならないと把握できない
(2)外注先に出ている移動の在庫が把握できない
といった問題点がありましたが、材料・仕掛・完成品・移動品がリアルタイムで在庫照会し、可能となりました。現在では、月1回の棚卸も実棚との差異がなくなり、ムダな在庫の削減ができました。さらに、納期遵守率も60%から100%に改善、業務改善と効率化を図ることができました。
これからは二次開発として、売上・原価改善に向けたシステム対応を行い、さらなる業務改善と効率化を目指していきたいと思います。
製品のご紹介
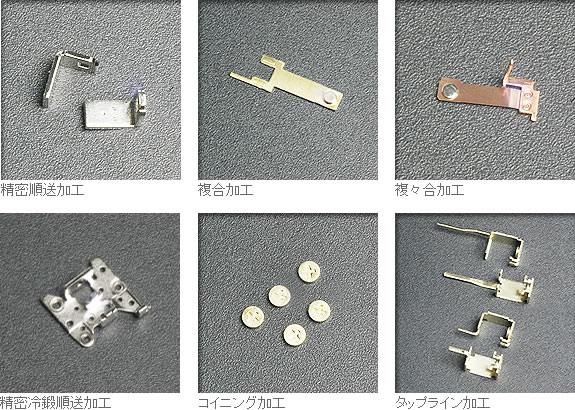
※記載の肩書きや数値、固有名詞はインタビュー時のものであり、変更されている可能性があることをご了承ください。
企業プロフィール
本社所在地 | 京都府亀岡市大井町南金岐重見46 |
---|---|
設立 | 2007年4月 |
資本金(万円) | 8,000 |
年商(百万円) | 2,064 <2014年3月> |
従業員数 | 89名 |
事業内容 | 金型設計製作及びプレス加工、自動機設計開発及び生産販売・納品・メンテナンス |
URL | http://www.taiyoaquris.co.jp/ |
